Contamination & Ingress:
In real-world use, products are exposed to a variety of chemicals on a daily basis. Fluid susceptibility testing evaluates how much damage is done by exposure to liquids, and how product design can help prevent failures by fluid contamination. Because most fluid contamination is caused by chemical spills or temporary exposure, our test methods are designed to replicate actual conditions as much as possible.
The Fluid Contamination (also known as Contamination by Fluids or Fluids Susceptibility) Testing process involves testing items in many different fluids in order to determine the possible breakdown of materials or coatings, which may occur during an item’s service life.
Envitest Lab provides fluid compatibility testing to a number of recognized industry standards and designs custom protocols to meet your specifications. Envitest Lab has dedicated testing chambers for acidic, Neutral, and base solutions available in order to evaluate equipment under test, as required by Military, automotive and commercial standards.
Our chambers can test to the following fluid types:
- Cleaning fluids
- Coolant dielectric fluids
- De-icing/Anti-freeze fluids
- Disinfectants
- Fire extinguishants
- Fuels
- Hydraulic fluids
- Insecticides
- Lubricating oils
- Solvents
Ingress Protection (IP) Testing:
Ingress Protection testing, or IP testing, determines a product’s susceptibility to solid particle ingress (sand or dust) as well as water ingress.
Envitest environmental simulation labs provide IP testing to specifications including JSS 55555, RTCA-DO-160 (avionics), MIL-STD’s (military), IEC/IS/EN 60529 & NEMA (electronics), as well as DIN and SAE standards (automotive). The Ingress Protection standard we most commonly test to is BS EN/IEC 60529.
Envitest Lab utilizes calibrated IP testing equipment, including immersion tanks, nozzles and dust specific to the IP rating required. Utilizing purpose built, walk-in test chambers, we are also able to test on very large components/enclosures. Our Engaged Experts can help with guidance and offer advice on custom testing methods to meet your requirements.
Dust and water can find their way inside a product at a layer that joins two parts. Therefore, layers between components are often sealed by a gasket — either a rigid or a flexible gasket.Many products require insulation from outside elements in order to function properly. Those outside elements include mist, steam, sprayed water, sand, oil and even fingers, just to name a few. Ingress protection testing helps determine whether a particular product is going to function appropriately when placed in the field.
Standards Followed for Contamination & Ingress
Ingress Protection (IP) Testing |
---|
BS EN 60529, ISO 20653 |
MIL-STD-810, MIL STD 202H |
EN 2591, ETSI EN 300 019 |
JSS 55555, JSS 5855 |
Capabilities Include:
Acoustic noise testing
Impact testing
Vibration testing
Shock testing
Drop testing
HALT testing
HASS testing
HATS testing
Materials fatigue testing
Bump/Bounce Testing
Quality Approved Lab









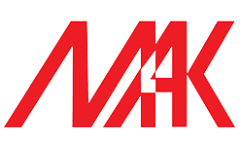
Case Studies
1. Understanding Ingress Protection (IP) Ratings: Shielding Enclosures from Harsh Environments
Introduction
In the world of engineering and equipment design, protection against environmental factors is utmost requirements. Many enclosures often find themselves in demanding conditions, where they must fend off the elements and external influences to keep sensitive components safe and functional. This is where Ingress Protection (IP) ratings come into play. The IP rating, defined by the international standard IEC 60529, serves as a universal language to gauge an enclosure’s ability to withstand ingress from solids and liquids. In this article, we will delve into the depths of IP ratings, deciphering their meaning and significance.
Decoding the IP Rating:
An IP rating always comprises the letters “IP” (Ingress Protection), followed by two digits and an optional letter. This alphanumeric code conveys vital information about the level of protection provided by the enclosure. Let’s break down the components of the IP rating and what they signify.
First Digit: Solids Protection
The first digit in the IP rating indicates the degree of protection an enclosure offers against the intrusion of solid foreign objects. It also takes into account the prevention of people accessing hazardous parts.
IP | 0 | X | This means there is no data available to specify a protection rating. It’s essentially an unknown or unclassified level of protection. |
IP | 1 | X | This rating provides protection against objects greater than 50 mm in diameter. It doesn’t offer defense against deliberate contact but keeps out any large surface of the body. |
IP | 2 | X | An IP rating of 2 safeguards against objects over 12.5 mm in diameter, making it suitable for preventing fingers or similar objects from accessing sensitive components. |
IP | 3 | X | With this rating, the enclosure offers protection against objects larger than 2.5 mm in diameter, making it resistant to tools, thick wires, and the like. |
IP | 4 | X | Enclosures with a rating of 4 provide protection against objects greater than 1 mm in diameter, ensuring most wires, screws, and similar items can’t penetrate. |
IP | 5 | X | This rating signifies that the enclosure is dust-protected, offering defense against dust ingress that could cause damage to the equipment’s operation. It also guarantees complete protection against contact. |
IP | 6 | X | An IP rating of 6 denotes that the enclosure is “dust-tight,” meaning it prevents any ingress of dust, no matter how fine, while also ensuring complete protection against contact. |
Second Digit: Liquids Protection
The second digit in the IP rating code reflects the level of protection an enclosure provides against the intrusion of water.
IP | X | 0 | Similar to the first digit, “X” indicates that there is no available data to specify a protection rating. |
IP | X | 1 | An enclosure rated at 1 offers protection against vertically falling water drops or dripping water. |
IP | X | 2 | With a rating of 2, the enclosure can fend off vertically falling water drops when tilted at an angle less than 15 degrees. |
IP | X | 3 | Enclosures rated at 3 can withstand water sprayed at an angle of less than 60 degrees from the vertical position. |
IP | X | 4 | This rating guarantees protection against water splashing against the enclosure from any direction. |
IP | X | 5 | Enclosures rated at 5 can endure water projected by a nozzle (6.3 mm) against the enclosure from any direction. |
IP | X | 6 | A rating of 6 signifies that the enclosure can withstand powerful water jets, specifically water projected in powerful jets from a 12.5 mm nozzle against the enclosure from any direction. |
IP | X | 7 | Enclosures rated at 7 can resist water ingress when temporarily immersed up to 1 meter. |
IP | X | 8 | With a rating of 8, the enclosure can endure water ingress when continuously immersed beyond 1 meter. |
IP | X | 9 | This rating involves close-range, high-pressure, and high-temperature spray downs for particularly harsh conditions. |
Why IP Ratings Matter:
Understanding IP ratings is vital for various industries and applications where enclosures are exposed to challenging environments. These ratings help engineers and designers select the right enclosures to ensure the longevity and reliability of equipment. Whether it’s a dusty manufacturing floor, a rainy outdoor setting, or a high-pressure cleaning environment, the appropriate IP rating ensures the continued functionality of vital components.
In conclusion, Ingress Protection (IP) ratings are a universal language for specifying the protective capabilities of enclosures. By analyzing the first and second digits of an IP rating, you can gain insights into how effectively an enclosure guards against solids and liquids. This knowledge empowers engineers and designers to make informed decisions when selecting the right equipment for a given application, ensuring that components remain safe and operational even in the harshest of conditions.
2. Enhancing Ingress Protection for Electrical Panels
Introduction
Ingress protection, often denoted as IP, is a critical consideration for electrical panels in various industries. Ingress protection measures safeguard electrical equipment from dust, water, and other foreign objects that can potentially cause damage or malfunction. This case study explores the importance of ingress protection for electrical panels and how a manufacturing facility overcame challenges to enhance the protection of their electrical panels.
Challenge
A manufacturing facility that specialized in precision machinery production faced recurring issues with their electrical panels. The facility was in an environment where it was exposed to a range of challenging conditions:
- Dust and Debris
- Moisture and Humidity
- Temperature Variations
These challenges were not only causing equipment failures but also leading to downtime, increased maintenance costs, and, in some cases, safety concerns. The facility recognized the urgent need to enhance the ingress protection of their electrical panels to ensure uninterrupted production and safety.

Solution
The manufacturing facility embarked on a comprehensive approach to address the ingress protection challenges. The facility requested Envitest Lab to provide a solution which overcomes the problem. By seeing the enclosure, first thing we recommended was test for Ingress Protection and see the results. If the enclosure is properly sealed and fit, all the above 3 stated problems will be solved. Test was carried out and found that the enclosure was not fit to used. We advised following to overcome the problem:
- Sealant and Gaskets: To combat dust and debris ingress, the sealing mechanisms and gaskets around electrical panel enclosures must be improved. This included employing specially designed silicon gaskets and applying sealant to eliminate gaps and crevices.
- Ventilation and Filtration: To prevent overheating while still maintaining ingress protection, we devised a ventilation system with dust filters. These filters ensured the ingress of air while blocking dust and debris.
- Re-Painting: To maintain the effectiveness of their ingress protection measures, we recommended to paint the enclosure with enamel (gloss) paint. This largely reduce the moisture build up inside the enclosure.
Results
The efforts to enhance ingress protection for electrical panels yielded several positive outcomes including the Reduced Downtime. The frequency of equipment failures and downtime significantly decreased as a result of improved ingress protection. Further overall safety of the facility improved, with a decrease in the risk of electrical malfunctions and accidents due to ingress-related issues. By addressing ingress issues, the facility reduced the need for costly repairs and replacements of electrical parts.
Conclusion: Enhancing ingress protection for electrical panels is crucial to ensure the reliability, safety, and longevity of electrical equipment in various industries. This case study demonstrates how a manufacturing facility overcame challenges related to dust, moisture, and temperature fluctuations by implementing a comprehensive strategy that included sealants, gaskets, enclosure ratings, and regular maintenance. By taking these steps, the facility significantly improved the reliability and safety of their electrical panels while reducing downtime and maintenance costs. This case study serves as a valuable example of the importance of addressing ingress protection issues in industrial settings.
3. Uncovering the Elusive Water Ingress during IPX6 Testing for Plastic Enclosures
Introduction
In the domain of product testing and quality assurance, ensuring the integrity of plastic enclosures is paramount. A leading manufacturer of electronic enclosures, adhering to international standards is a non-negotiable aspect of their commitment to product excellence. This case study explores into a challenging encounter during the IPX6 testing of plastic enclosures, highlighting how a determined team overcame unexpected water ingress to ensure the reliability and compliance of their products.

Customer was in the final stages of conducting IPX6 testing for their electronic enclosures as per the IEC60529 standard. The precision and attention to detail were evident in the quality of their materials and assembly of the enclosures. However, during the IPX6 testing, which evaluates protection against powerful water jets, an unexpected issue emerged. Water ingress occurred, compromising the enclosure’s integrity and raising a significant red flag.
The situation was puzzling. The enclosure’s assembly was impeccable, and the materials used were of the highest quality. The team was determined to uncover the source of this intrusion and address it promptly to maintain the product’s credibility.
Investigation:
We embarked on a relentless investigation to pinpoint the water entry point. The process involved multiple tests and meticulous examination of the enclosure. The team revisited every step of the assembly process, scrutinized materials for any potential weaknesses, and reviewed the testing procedure to ensure it was conducted correctly.
Over time, the team discovered that the water ingress was not the result of a manufacturing flaw, but rather, it stemmed from a concealed path that was difficult to detect. This mysterious entry point had allowed water to penetrate the enclosure, even though the materials and assembly had held up admirably.
Resolution
Through persistent investigation and problem-solving, plastic successfully resolved the issue. Envitest lab team identified the precise location of the water ingress and took immediate corrective action to rectify it. This not only restored the enclosure’s integrity but also ensured compliance with the IPX6 standard. This case study was a testament to the importance of rigorous testing and the relentless pursuit of quality in product development. It demonstrates that even the most meticulous preparations can encounter unexpected challenges, but with dedication and perseverance, these challenges can be overcome, leading to stronger, more reliable products.
The Outcome: Although the challenge was significant, the lessons learned from this experience were invaluable. Following the resolution of the water ingress issue, all subsequent tests for plastic’s enclosures proceeded smoothly without any further complications. Envitest lab’s commitment to quality and determination to address unexpected challenges underscored their dedication to delivering reliable and compliant products to our customers.
Excellent
Based on 40 reviews

Have been here many a times as technology partner. The business has dynamic people experts in their subject. Growing rapidly, this is a partner you want to have for product testing.
Nitin Mangesh
Test lab for environmental testing of electronic hardware. There is scope for interior premises improvement in ground floor lab area..
NataRaju Kothuru
This lab is located somewhere nearby Garebhavipalya next to maruthi timbers this is environment test is done for all defense unit for various companies..
SNUF ADD
Professional with clients and good for startups to test the product reliability.
Aravind Singh
Very nice lab with a professional and very friendly staff…
Shreyas Gakka
// Certifications
State-of-the-Art Laboratories
Envitest is the world’s most trusted independent test, inspection, and certification company. With state-of-art lab and the top thought leaders, Envitest provides customers with best-in-class testing services to serve a wide range of industries, including space, defense, automotive, energy, electronics, telecommunications, medical, IoT, industrial, and aviation.
Working as a trusted extension of your engineering team, we stay connected during every phase of your project and we deliver accurate and timely results.
// FAQ’s